Zuigerveren hebben een grote verscheidenheid aan materialen en verschillende eigenschappen. Bij de keuze van het zuigerveermateriaal moet rekening worden gehouden met de gebruiksomstandigheden, prestatie-eisen, het type veer en andere factoren. Over het algemeen moet het zuigerveermateriaal van een verbrandingsmotor aan de volgende eisen voldoen:
1. Hoog genoeg mechanische sterkte bij hoge temperaturen
2. Slijtvastheid en lage wrijvingscoëfficiënt
3. Het is niet eenvoudig om hechting te bewerkstelligen en gemakkelijk in te lopen
4. De verwerking is handig en de prijs is goedkoop
Op deze manier moet het zuigerveermateriaal een bepaalde sterkte, hardheid, elasticiteit, slijtvastheid (inclusief olieopslag), corrosieweerstand, thermische stabiliteit en verwerkbaarheid hebben. Momenteel is het materiaal van de zuigerveer voornamelijk gietijzer. Met de versterking van de motor is er een trend van overgang van grijs gietijzer naar smeedbaar gietijzer, nodulair gietijzer en staal. Zie tabel 2-1 voor veel voorkomende materialen en eigenschappen.
Tabel 2-1 veel voorkomende materialen en eigenschappen van zuigerveren
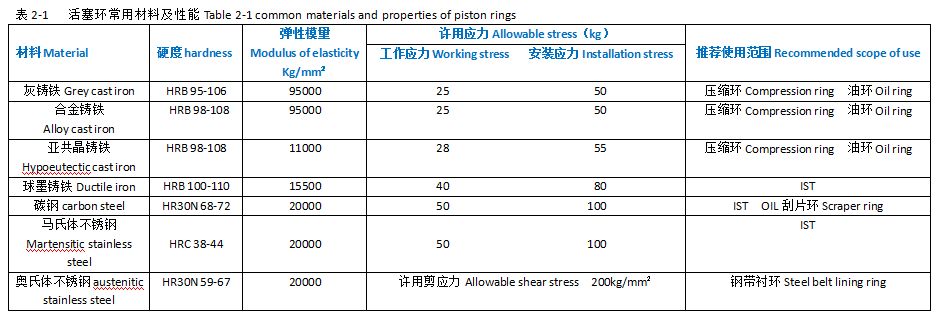
De introductie van vandaag is echter niet de zuigerveer van gewone materialen, maar de zuigerveer van metaal-keramische composietfilm (keramische geïnfiltreerde zuigerveer of kortweg keramische metalen zuigerveer), hierna metaal-keramische zuigerveer genoemd.
Cermet-zuigerveren worden gemaakt door boornitride (onderdeel van kubisch boornitride) keramiek met * zelfsmerende functie in de oppervlaktelaag van het zuigerveerwrijvingspaar te infiltreren bij lage temperatuur (onder 200 ℃) door gebruik te maken van 's werelds * geavanceerde "plasma chemische damp deposition technology", zodat de werkoppervlaktelaag van zuigerveren keramisch is. De zuigerveren na keramische infiltratie hebben een goede slijtvastheid, slijtvastheid en corrosieweerstand. Daarom kan de levensduur van de zuigerveer worden verbeterd. Het composietkeramiek wordt in het oppervlak van de zuigerveer geïnfiltreerd door plasma-chemische dampafzetting, wat anders is dan het keramische spuitproces op het oppervlak van andere zuigerveren. Deze procesmethode kan ervoor zorgen dat het keramische composietmateriaal een stevige hechtkracht heeft met het oppervlak van de zuigerveer zonder te barsten en eraf te vallen.
Bovendien heeft de cermet-composietlaag een elektronische structuur die lijkt op rhodium, waardoor deze verbrandingskatalyse in de motor kan uitvoeren en het emissiegehalte van CO en HC aanzienlijk kan verminderen. Daarom hebben keramisch geïmpregneerde zuigerveren ook een katalytische werking.
De "Cermet-composietfilm"-technologie heeft de* beoordeling in 1997 doorstaan.
Keramisch geïmpregneerde zuigerveren worden op grote schaal gebruikt in grote motorfabrieken met een goed toepassingseffect.
Het vormt "functioneel keramiek", gemengd met metalen, dat de uitstekende eigenschappen heeft van een hoge oppervlaktehardheid, een lage wrijvingscoëfficiënt, slijtagevermindering en een lange levensduur.
Bij lage temperaturen (lager dan 200 ℃) wordt nitride (keramisch composietmateriaal) in het gereedschapsoppervlak geïnfiltreerd door plasma-chemische dampafzetting.
Functies:
1. Groei bij lage temperaturen. Wanneer de filmvormingstemperatuur lager is dan 200 ℃, zal dit het substraat en het oppervlak van het werkstuk niet beschadigen, noch het werkstuk vervormen, en zal het de bewerkingsnauwkeurigheid en assemblageprestaties niet beïnvloeden.
2. De verbinding is stevig. Omdat het metaal met boornitride en kubisch boornitride in de toestand van vacuümplasma diffundeert om functionele gradiëntmaterialen te vormen, zullen de composietfilms niet loslaten bij hoge temperaturen of schokken.
3. Zowel de hardheid als de taaiheid zijn verbeterd. Door de tweefasige diffusie van composietfilm en metaal om functioneel materiaal met een hellende gradiënt te vormen, speelt het niet alleen de rol van een stevige combinatie van de overgangslaag, maar verbetert het ook de hechtsterkte, trekcapaciteit en buigweerstand van keramiek, en de taaiheid ervan. overtreft die van keramiek zelf.
4. Goede slijtvastheid bij hoge temperaturen. De experimentele resultaten laten zien dat, vergeleken met verchromen, de hardheid van de composietfilm sterk toeneemt met de temperatuurstijging in de omgeving van 250 ℃ - 350 ℃, en dat de oppervlaktehardheid met meer dan hv210 toeneemt, terwijl het harde chroom daarna aanzienlijk afneemt. 250 ℃, en neemt af met ongeveer hv110 bij 350 ℃. Dus vergeleken met het werkstuk zonder composietfilmplating heeft het keramisch geplateerde werkstuk een betere slijtvastheid bij hoge temperaturen.
5. Sterke oxidatieweerstand. De experimentele resultaten laten zien dat de composietfilm nog steeds een goede oxidatieweerstand en zuur-base-resistentie heeft wanneer de temperatuur hoger is dan 1000 ℃.
6. Het heeft de functie van oxidatie en katalyse. Wanneer het keramiek in het metaaloppervlak dringt, wordt een geschikte hoeveelheid elektronenvacature gegenereerd, waardoor de composietfilm een oxidatiekatalytisch effect heeft op CO en HC, en de uitlaatemissievervuiling van de motor aanzienlijk wordt verminderd.
7. Goede wikkel- en plateerprestaties. Composietfilms zijn chemische dampafzetting, dus composietfilms kunnen overal worden gekweekt waar gas doorheen kan gaan, en de verwerkingsomstandigheden worden niet beperkt door de vorm en positie van het werkstuk.
8. Brede toepassingsgebieden. De composietfilm wordt niet alleen op de motor aangebracht, maar is ook geschikt voor de wrijvingsparen van verschillende machines, hoge temperatuur- en corrosiebestendige onderdelen, verschillende snijgereedschappen en mallen, en kan zich aanpassen aan verschillende metalen of niet-metalen materialen door middel van verschillende procesparameters.