Kolbenringe weisen eine große Materialvielfalt und unterschiedliche Eigenschaften auf. Bei der Auswahl des Kolbenringmaterials sollten dessen Betriebsbedingungen, Leistungsanforderungen, Ringtyp und andere Faktoren berücksichtigt werden. Im Allgemeinen muss das Kolbenringmaterial von Verbrennungsmotoren die folgenden Anforderungen erfüllen:
1. Ausreichend hohe mechanische Festigkeit bei hohen Temperaturen
2. Verschleißfestigkeit und niedriger Reibungskoeffizient
3. Es ist nicht einfach, Haftung zu erzeugen und leicht einzulaufen
4. Die Verarbeitung ist bequem und der Preis ist günstig
Auf diese Weise muss das Kolbenringmaterial eine bestimmte Festigkeit, Härte, Elastizität, Verschleißfestigkeit (einschließlich Öllagerung), Korrosionsbeständigkeit, thermische Stabilität und Verarbeitbarkeit aufweisen. Derzeit besteht das Material des Kolbenrings hauptsächlich aus Gusseisen. Mit der Weiterentwicklung des Motors gibt es einen Trend zum Übergang von Grauguss zu Temperguss, Sphäroguss und Stahl. Gängige Materialien und Eigenschaften finden Sie in Tabelle 2-1.
Tabelle 2-1 gängige Materialien und Eigenschaften von Kolbenringen
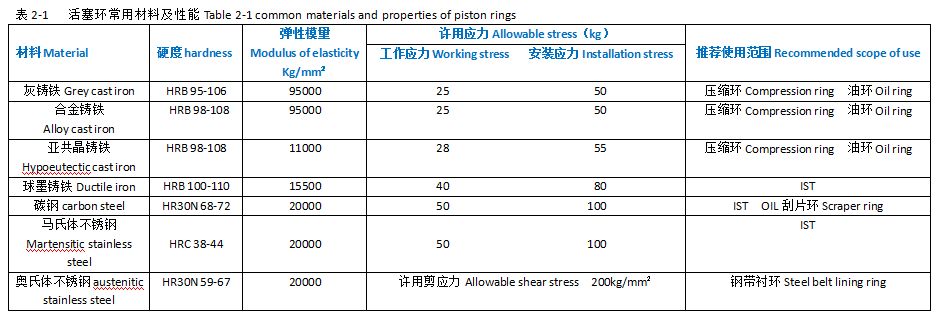
Die heutige Einführung ist jedoch nicht der Kolbenring aus gängigen Materialien, sondern der Metall-Keramik-Verbundfilm-Kolbenring (Keramik-infiltrierter Kolbenring oder kurz Keramik-Metall-Kolbenring), im Folgenden als Metall-Keramik-Kolbenring bezeichnet.
Cermet-Kolbenringe werden durch Infiltration von Bornitrid-Keramik (Bestandteil des kubischen Bornitrids) mit selbstschmierender Funktion in die Oberflächenschicht des Kolbenring-Reibungspaares bei niedriger Temperatur (unter 200 °C) unter Verwendung des weltweit fortschrittlichsten „Plasma-Chemiedampfes“ hergestellt Abscheidungstechnologie", so dass die Arbeitsoberfläche der Kolbenringe aus Keramik besteht. Die Kolbenringe weisen nach der Keramikinfiltration eine gute Verschleißfestigkeit, Verschleißfestigkeit und Korrosionsbeständigkeit auf, wodurch die Lebensdauer des Kolbenrings verbessert werden kann. Die Verbundkeramik wird durch plasmachemische Gasphasenabscheidung in die Oberfläche des Kolbenrings infiltriert, was sich vom Keramikspritzverfahren auf der Oberfläche anderer Kolbenringe unterscheidet. Durch diese Prozessmethode kann erreicht werden, dass das Verbundkeramikmaterial eine feste Bindungskraft mit der Oberfläche des Kolbenrings hat, ohne dass es zu Rissen oder Abfallen kommt.
Darüber hinaus verfügt die Cermet-Verbundschicht über eine rhodiumähnliche elektronische Struktur, sodass sie eine Verbrennungskatalyse im Motor durchführen und den Emissionsgehalt von CO und HC erheblich reduzieren kann. Daher haben mit Keramik imprägnierte Kolbenringe auch eine katalytische Wirkung.
Die „Cermet-Verbundfolie“-Technologie hat 1997 die *-Prüfung bestanden.
Mit Keramik imprägnierte Kolbenringe werden in großen Motorenwerken häufig mit guter Anwendungswirkung eingesetzt.
Es bildet mit Metallen verbundene „Funktionskeramiken“, die sich durch hohe Oberflächenhärte, niedrigen Reibungskoeffizienten, Verschleißminderung und lange Lebensdauer auszeichnen.
Bei niedrigen Temperaturen (unter 200 °C) wird Nitrid (Verbundkeramikmaterial) durch plasmachemische Gasphasenabscheidung in die Werkzeugoberfläche infiltriert.
Merkmale:
1. Wachstum bei niedriger Temperatur. Wenn die Filmbildungstemperatur unter 200 °C liegt, werden das Substrat und die Oberfläche des Werkstücks nicht beschädigt, das Werkstück wird nicht verformt und die Bearbeitungsgenauigkeit und Montageleistung werden nicht beeinträchtigt.
2. Die Verbindung ist fest. Da das Metall im Vakuumplasmazustand mit Bornitrid und kubischem Bornitrid diffundiert und Materialien mit abfallendem Funktionsgradienten bildet, lösen sich die Verbundfilme bei hohen Temperaturen oder Stößen nicht ab.
3. Sowohl Härte als auch Zähigkeit werden verbessert. Aufgrund der zweiphasigen Diffusion von Verbundfolie und Metall zur Bildung eines Funktionsmaterials mit geneigtem Gradienten spielt es nicht nur die Rolle einer festen Verbindung der Übergangsschicht, sondern verbessert auch die Haftfestigkeit, Zugfestigkeit und Biegefestigkeit von Keramik sowie deren Zähigkeit übertrifft die von Keramik selbst.
4. Gute Verschleißfestigkeit bei hohen Temperaturen. Die experimentellen Ergebnisse zeigen, dass im Vergleich zur Verchromung die Härte des Verbundfilms mit steigender Temperatur in einer Umgebung von 250 °C bis 350 °C stark zunimmt und die Oberflächenhärte um mehr als hv210 zunimmt, während der Hartchromgehalt danach deutlich abnimmt 250 ℃ und nimmt bei 350 ℃ um etwa hv110 ab. Verglichen mit dem Werkstück ohne Verbundfilmbeschichtung weist das keramikbeschichtete Werkstück daher eine bessere Verschleißfestigkeit in Hochtemperaturumgebungen auf.
5. Starke Oxidationsbeständigkeit. Die experimentellen Ergebnisse zeigen, dass die Verbundfolie auch bei Temperaturen über 1000 °C immer noch eine gute Oxidationsbeständigkeit und Säure-Base-Beständigkeit aufweist.
6. Es hat die Funktion der Oxidation und Katalyse. Wenn die Keramik in die Metalloberfläche eindringt, wird eine entsprechende Menge an Elektronenleerstellen erzeugt, wodurch der Verbundfilm eine oxidative katalytische Wirkung auf CO und HC hat und die Abgasemissionen des Motors erheblich reduziert.
7. Gute Wickel- und Beschichtungsleistung. Bei Verbundfolien handelt es sich um chemische Gasphasenabscheidung, sodass Verbundfolien überall dort aufgewachsen werden können, wo Gas durchströmen kann, und die Verarbeitungsbedingungen nicht durch die Form und Position des Werkstücks eingeschränkt sind.
8. Breite Anwendungsbereiche. Die Verbundfolie kann nicht nur auf den Motor aufgetragen werden, sondern eignet sich auch für die Reibpaarungen verschiedener Maschinen, hochtemperatur- und korrosionsbeständiger Teile, verschiedener Schneidwerkzeuge und Formen und kann sich durch verschiedene metallische oder nichtmetallische Materialien anpassen unterschiedliche Prozessparameter.